The Ultimate Guide to Construction Cost Analysis
Introduction
In construction, as in any business, it all comes down to the dollars and cents.
But a unique combination of large numbers and long timeframes make construction a particularly challenging industry for the lucky few charged with calculating and managing costs.
Enter construction cost analysis: the process of assessing and monitoring expenses to effectively manage the project budget, helping you to prioritise spend, identify savings, and generally make better fiscal decisions.
In this guide we’ll take a deep dive into the world of construction cost analysis: what it is, why it’s important, and how your construction business can make the most of it.
Key takeaways
- Cost analysis is an exercise in budget responsibility, and plays a pivotal role in the construction industry.
- Cost analysis grants a clearer picture of project finances, helps to identify cost savings and enhance profitability, and can minimise project delays.
- Construction costs can either be direct (materials, labour, equipment) or indirect (admin, corporate, general overheads)
- Three main factors influence construction costs: economic, regulatory and environmental.
- There are three basic construction cost analysis methods: elemental analysis, comparative analysis and parametric estimation.
- Accuracy can be enhanced by combining cost analysis methods and utilising advanced techniques like value engineering and life-cycle costing.
The role of cost analysis in construction
Construction cost analysis identifies where you are currently spending your money and resources on a project, and whether this spend is as good as it could be. The goal: ensure the allocation of money and resources delivers the maximum possible return.
Construction cost analysis is performed before a project begins (i.e. during the estimation, quoting and bidding phase), and once work has begun, to ensure costs don’t overrun and stay within budget wherever possible. This helps to ensure returns are maximised over the life of the project.
Cost analysis is critical in construction, as projects tend to be defined by tight margins and extended time frames. You need to develop an accurate analysis from the get-go to ensure you quote appropriately and that costs don’t blow out over time.
Effective cost analysis considers how a range of factors (economic, regulatory and environmental) will influence project costs. It helps you to identify budget issues early, and gives you the insights you need to optimise resource allocation. Ultimately it ensures a project is managed successfully.
Key cost analysis stat
In 2020, 44.9% of new residential dwellings cost more to build than they were approved for. 22.5% of dwellings cost less.
Types of construction costs
Direct costs
As the name suggests, direct costs can be directly linked to a construction project. These costs come in four main forms:
- Materials - The physical resources that are used in the construction, from raw materials like cement, steel and timber through to fixtures, fittings and even decor.
- Labour - The wages and salaries of your own workers.
- Subcontractors - Payments to third parties hired to deliver specialised services.
- Equipment - The hired or purchased resources used to complete the project, from machinery to safety equipment to temporary structures.
Other direct costs include site preparation, permits and fees, transportation, inspection and land acquisition. Direct costs constitute the majority of construction costs.
Indirect Costs
Indirect costs are those that can’t be directly attributed to the construction project, but that still play a vital role in its successful completion. Indirect costs are many and varied, and may include:
- General overhead - General operational expenses for the construction company, such as office rent, utility bills and supplies.
- Admin salaries - The wages and salaries of workers in areas like management, HR, accounting, sales and marketing.
- Corporate resources - Costs such as software, office equipment, travel and training.
How to prevent cost overrun in construction projects
Construction cost analysis methods
Elemental analysis
The elemental analysis method involves breaking down a project into its separate parts and assigning costs to each element.
This detailed approach allows for a granular examination of project expenses, providing clarity on where the bulk of the budget is allocated.
By categorising costs by element, such as materials, labour, equipment and overheads, project managers gain insights into which areas are driving expenditure. Additionally, elemental analysis facilitates accurate budgeting and cost forecasting, enabling better financial management throughout the project lifecycle.
However, this method can be time-consuming and requires extensive data collection and categorisation to ensure accuracy and reliability.
- Accuracy: High when source data is reliable and estimates are generated by experts.
- Used for: Complex, nuanced and unique projects where detailed cost breakdowns are required.
Comparative analysis
In the comparative analysis method, costs are determined by comparing the current project with past projects of similar size, type, scope and complexity.
This real-world comparison not only helps in understanding costs but also in identifying cost influences, trends, patterns and drivers. Incorporating cost codes into this analysis can enhance its accuracy by providing a more granular breakdown of expenses.
However, it may be challenging to find comparable projects, and this analysis may not fully account for the unique aspects of the current project.
- Accuracy: Reliant on access to relevant data from comparable projects.
- Used for: Conventional, recurrent projects that feature minimal unique aspects and align with standard industry practices.
Parametric estimation
The parametric estimation method relies on statistical models to forecast how specific project features (like square metreage, building height and complexity) influence construction costs, generating estimates based on these factors.
While this approach is fast and streamlined, its accuracy hinges on the quality of the input data – in other words, the better the data, the better the estimates.
- Accuracy: Reliant on access to relevant data from comparable projects.
- Used for: Projects that feature repetitive elements and where clear parameter-cost relationships exist.
No matter which of these methods you utilise, all demand accurate data and benchmarks, professional expertise and adjustments for project-specific factors.
Pro tip
Use multiple cost analysis methods
The cost analysis methods described don’t exist in siloes. Each has different strengths and weaknesses, so there may be situations in which all three are used within the same project. This can result in a far more accurate picture of construction costs.Advanced cost analysis techniques
There are also a number of advanced techniques that can serve to enhance your cost analysis efforts. These include:
- Value engineering: The practice of searching for alternatives that offer better functionality at a lower cost, thereby guaranteeing your project gains maximum value from any spend.
- Life-cycle costing: An element of value engineering, this technique considers the total cost of a structure, material or piece of equipment over the course of its useful life. This helps to clarify the best long-term investment options.
- Building information modelling (BIM): A digital representation of physical and functional characteristics of a facility, BIM is used to generate insights and help make decisions over the course of the facility’s lifecycle.
These techniques are designed to generate data and insights that offer more clarity over costs. The ultimate aim is to maximise accuracy, and minimise the influence of guesswork and gut feel.
Construction Cost Codes: How You Can Use Them to Boost Profit
Factors that affect construction costs
Economic factors
Construction costs are significantly impacted by economic conditions, which can fluctuate widely. From the availability of local labour to global supply chain disruptions, economic factors play a crucial role.
For instance, during the COVID-19 pandemic, supply shortages coupled with increased demand led to unprecedented spikes in construction material prices.
Similarly, changes in interest rates can directly affect project costs financed through debt.
Regulatory factors
Local laws, rules and building codes profoundly impact construction projects. While they can be easy enough to plan for in theory, in practice it can be quite complex, as building codes can vary from location to location, and the rules can change at any time.
Obtaining necessary approvals can further complicate cost analysis, extending project timelines by weeks, months or even years.
Environmental factors
During the planning stage, a project might necessitate an environmental impact assessment to assess potential environmental effects. If adverse effects are identified, costs may arise from proposed solutions.
Additionally, the project might require the development and execution of an ongoing environmental management plan, adding extra costs.
Key moments in cost analysis
During COVID supply chain issues flipped construction upside-down almost overnight, turning basic materials into scarce and costly commodities, and causing major disruption as companies attempted to adjust to skyrocketing costs.
The 4 major benefits of construction cost analysis
1. Accurate quoting = enhanced profitability
Accurate construction cost analysis ensures precise project quoting. When your estimates align closely with actual costs, you enhance profitability by avoiding underquoting.
This means you can set competitive yet sustainable prices for your services, increasing the likelihood of winning bids without sacrificing profit.
While unexpected costs will always arise, leveraging robust cost analysis sets you in the best possible spot to start saying bye-bye to project cost overruns.
2. Gain a clearer financial picture
By conducting thorough cost analysis, you gain insights that provide a clearer picture of your financial standing. Here’s how:
- Identify cost trends: Through detailed analysis, you can uncover patterns and trends in your project expenses. This allows you to anticipate future costs more accurately and adjust your budget accordingly, helping you avoid surprises down the line.
- Evaluate project performance: By analysing project costs, you can assess the performance of individual projects or your entire portfolio. You can identify which projects are delivering the best return on investment and which ones may need adjustments to improve profitability.
- Inform strategic decision-making: Armed with comprehensive cost analysis data, you can make strategic decisions with confidence. Whether it’s deciding on future project investments, negotiating contracts with clients or suppliers, or adjusting resource allocation, you’ll have the insights needed to make sound financial choices that drive your business forward.
3. Identify potential cost savings
Construction cost analysis enables you to identify potential cost-saving opportunities throughout the project lifecycle.
By scrutinising expenses and exploring alternative approaches, you can pinpoint areas where efficiency improvements or strategic adjustments can lead to substantial savings.
This proactive approach to cost management ensures that you not only control your budget effectively but also optimise your resources for better financial outcomes.
4. Minimise project delays
Effective cost analysis goes beyond budget monitoring; it plays a crucial role in minimising project delays.
Through a detailed examination of costs, you can identify potential bottlenecks, resource shortages or inefficiencies that may lead to delays.
This foresight allows you to take proactive measures to keep your projects on schedule. The result is improved project timelines, enhanced client satisfaction and a reputation for timely and reliable project delivery. Now, that’s a win-win-win!
Why Simplifying Construction Cost Management is Critical
How Lentune makes your cost analysis smarter
With Lentune, you gain a suite of powerful tools designed to elevate your cost analysis game and drive better decision-making. Here’s how Lentune can totally transform your approach to cost analysis:
Project cost management: Lentune provides robust project cost management capabilities, empowering you with customisable cost codes tailored to your business’s specific needs. Whether you require detailed granularity or broader categorisation, Lentune’s flexible cost codes allow you to track expenses with precision.
Integration with cost estimation: Seamlessly integrate your cost estimation process with Lentune’s cost codes to compare actual project costs against the budget. By aligning estimates with cost codes, you gain valuable insights into project performance and identify discrepancies early on.
Purchase automation: With Lentune Purchase Automation, you gain real-time visibility into project commitments as they’re raised, rather than waiting for them to be processed. This live view of project costs allows you to spot budget creep before it blows out.
Centralised project data: By leveraging multiple Lentune modules such as invoice automation, timesheets and expense tracking, you consolidate all project data in one centralised platform. This unified view provides a holistic perspective of your project’s financial health, with costs synced automatically to your projects through seamless automation.
Cost analysis case studies
BLR Provincial Construction
Since 2008 BLR Provincial Construction has been delivering large-scale renovations and new builds across Victoria, and has built a reputation for quality. Unfortunately they faced administrative challenges, particularly in terms of the accuracy and efficiency of their monthly cost-plus reporting, which kept their Administration Manager working until 2am some weekends.
They have since implemented Lentune, which has automated huge swathes of formerly manual processes, and offers up accurate financial data in real time, enabling ongoing construction cost analysis. BLR can now make informed decisions, and can price more confidently, bid more competitively, and ultimately secure more projects.
Cook Brothers
Cook Brothers, a prominent construction company in New Zealand renowned for its track record of delivering top-notch projects on time and within budget, faced a common challenge: managing costs across multiple offices nationwide. As their operations expanded, so did the complexity of cost analysis and management.
Lentune came to the rescue. Integrated supplier pricing books allow team members to simply select the relevant product in a click, and know that the price is right. Ultimately Cook Brothers aim to have all their costs and expenses, from accounts payable to credit cards, in the one place, making construction cost analysis and management so much simpler and more streamlined.
Conclusion
Construction cost analysis serves as a cornerstone in ensuring the success of construction projects. By considering every financial factor and providing actionable strategies, it gives you an unparalleled understanding and command over project costs.
With the right methodologies and tools at your disposal, you can effectively monitor project expenses, pinpoint financial challenges and mitigate potential delays.
While uncertainties may persist in project financial management, employing high-quality construction cost analysis enables you to manage the variables within your control, safeguarding your business interests and fostering growth.
How we can help
At Lentune, we build smarter construction software to liberate your financial workflows. Our project cost management software puts all your numbers in one place, so you can say bye-bye to overruns. We’d love to show you how it works!
In a live demo, we can answer any questions and show you how Lentune could grow your business.
Frequently asked questions (FAQs)
Cost-benefit analysis is a method used to assess the viability of a project by weighing its expected costs against its anticipated benefits. This technique is crucial for decision-making, as it allows stakeholders to ensure that projects align with organisational objectives and deliver optimal value.
This process can be summarised in the following five steps:
- Identify project scope: Clearly outline the purpose of the cost-benefit analysis and gain a detailed understanding of essential project aspects, including timelines, constraints and resource requirements.
- Identify costs: Conduct a detailed cost analysis using the methods outlined in this guide.
- Identify benefits: Outline and measure the benefits the project is expected to yield, ranging from tangible aspects like property sales profits to intangible factors such as improved site safety.
- Compare costs and benefits: Execute the cost-benefit analysis by subtracting the identified costs from the anticipated benefits, determining the net benefit of the project.
- Make a decision: Based on the insights generated by the analysis, make an informed decision regarding the project's viability. Consider factors such as the magnitude of the net benefit, the risk associated with the project and its alignment with your organisational goals and priorities.
Accurately estimating the cost of a construction project requires access to accurate data. Modern cost analysis tools, such as Lentune, offer real-time updates, ensuring the accuracy of your estimates. By leveraging these tools, you can streamline the cost analysis process and minimise the margin of error in your estimates.
The process of preparing a construction cost analysis can be summarised in the following five steps:
- Implement cost analysis tools into your tech stack.
- Choose your preferred cost analysis method/s and any advanced analysis techniques you might utilise.
- Identify all the relevant costs for the project.
- Identify the factors that may influence your costs, and take potential effects into account.
- As the project moves forward, update your cost analysis to ensure you always enjoy a near-real time view of project finances.
Discover more from the blog
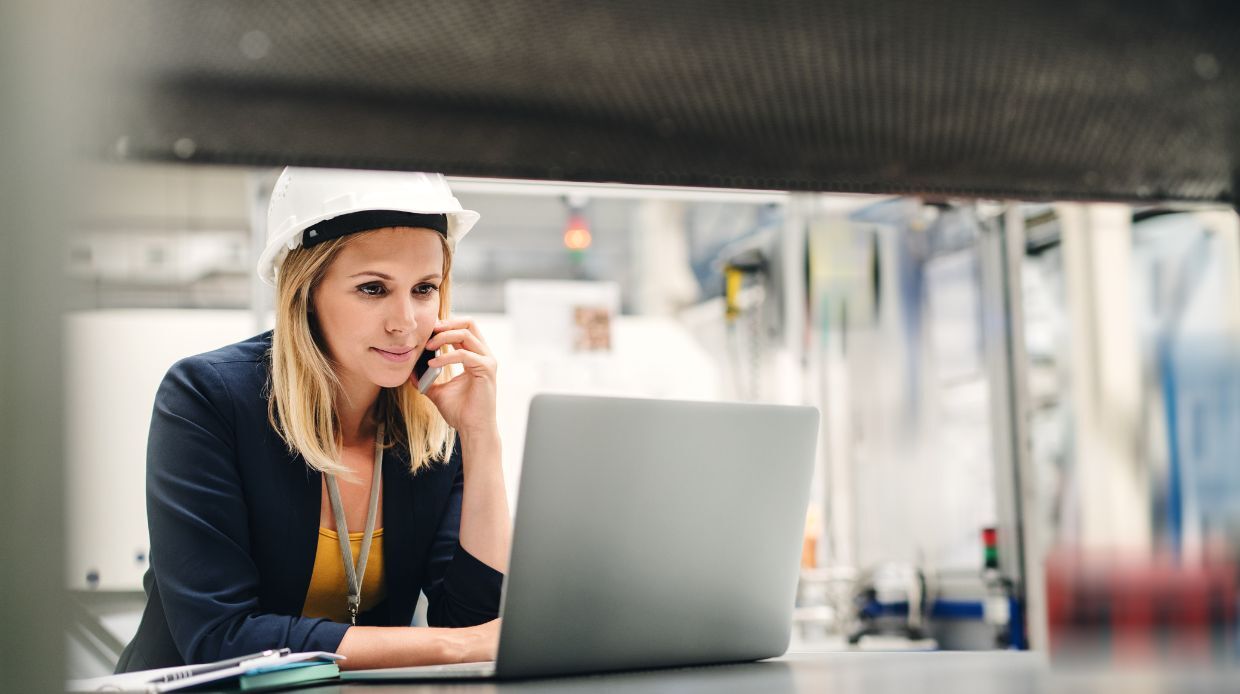
Why is Your Construction Business Losing Money? Start Here
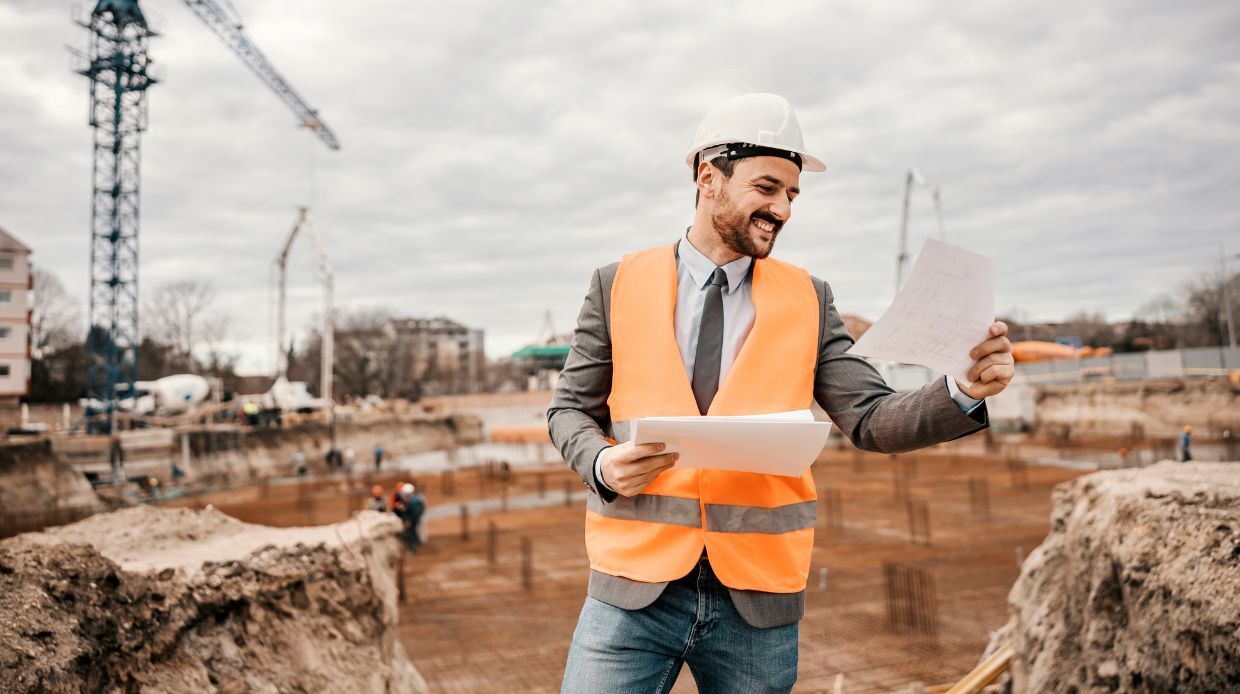
The 4 Financial Reports Every Construction Finance Team Needs
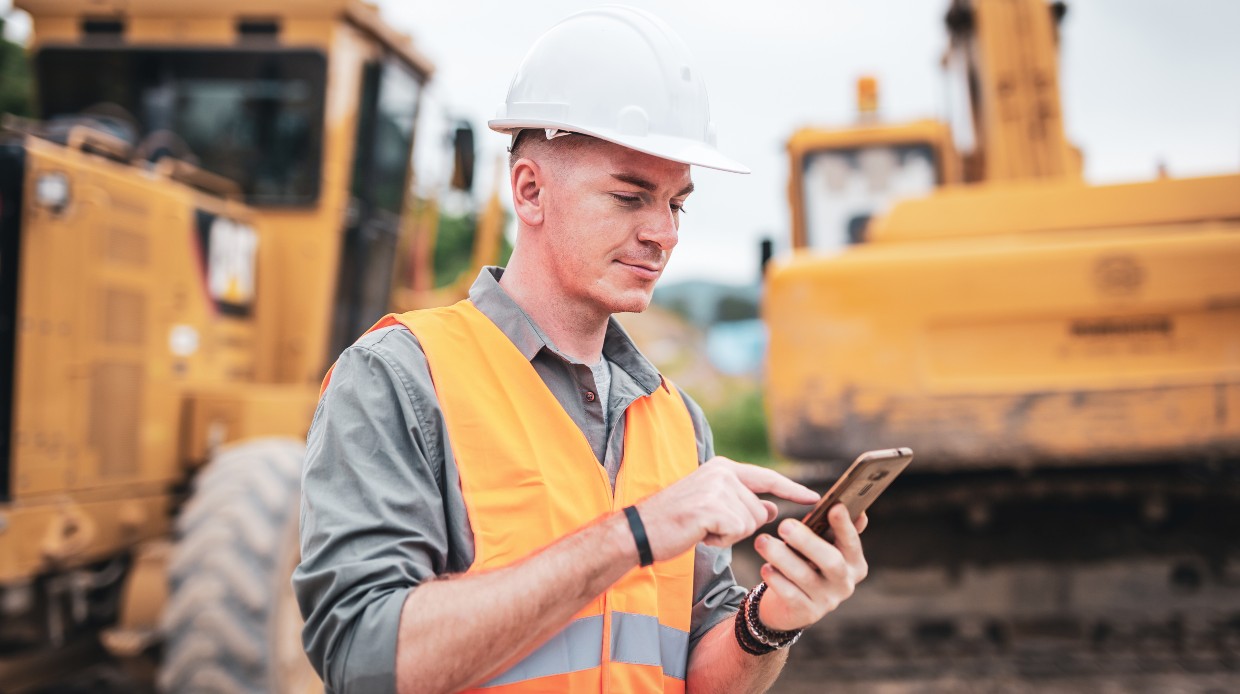